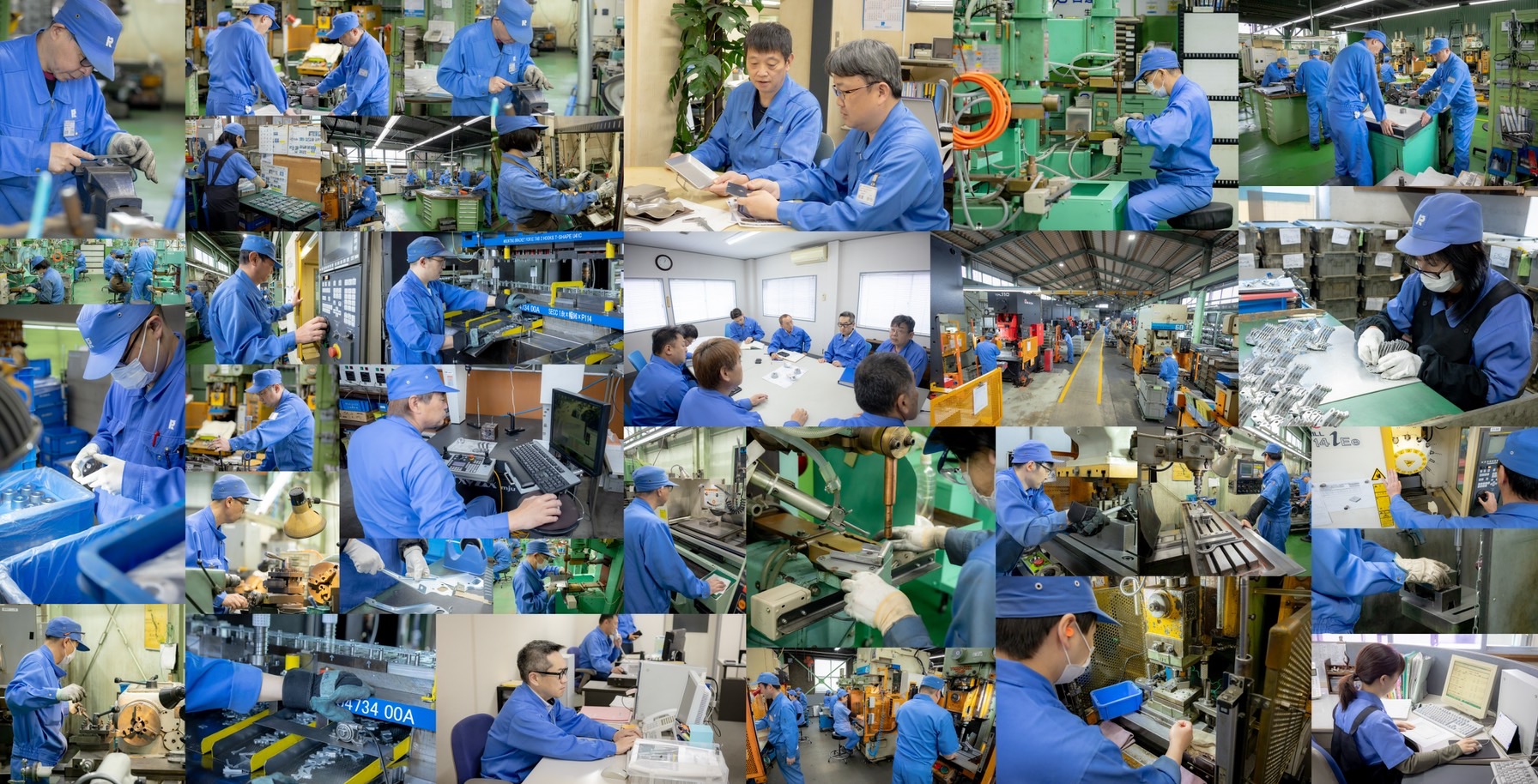
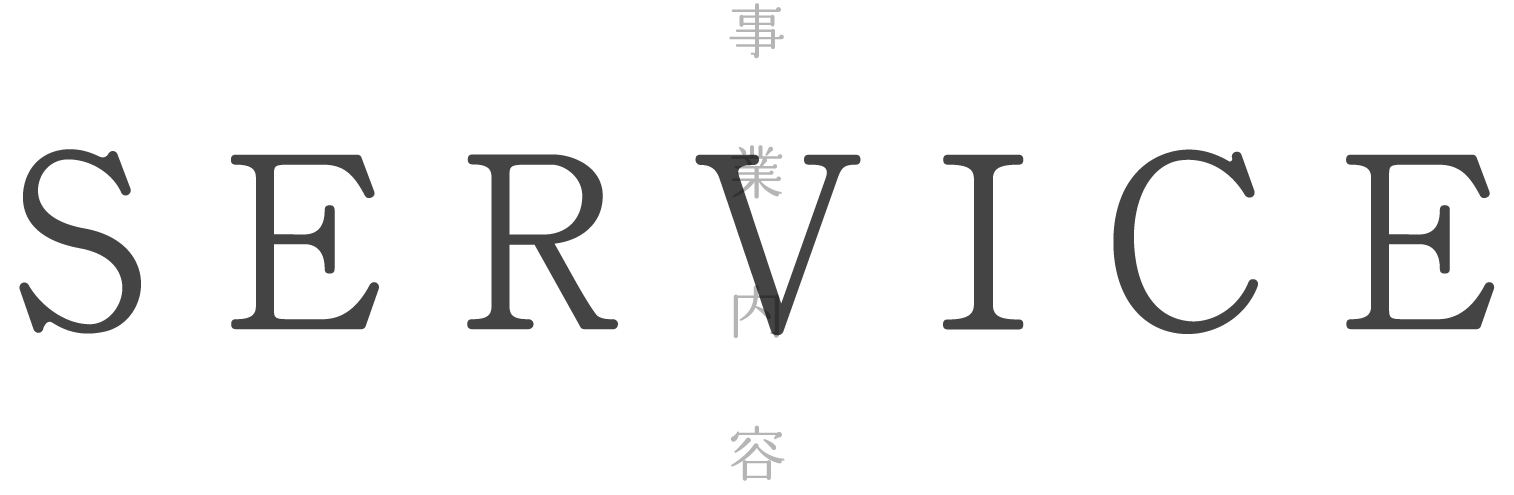
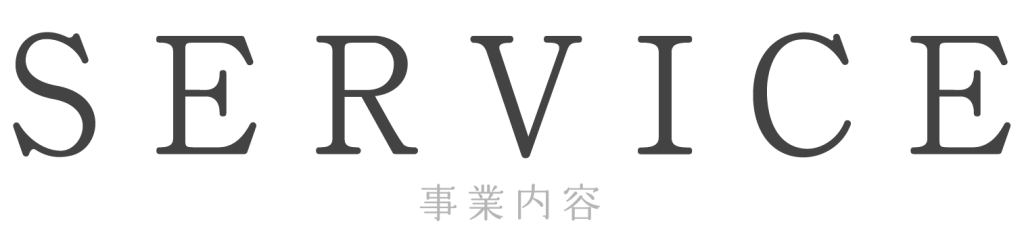
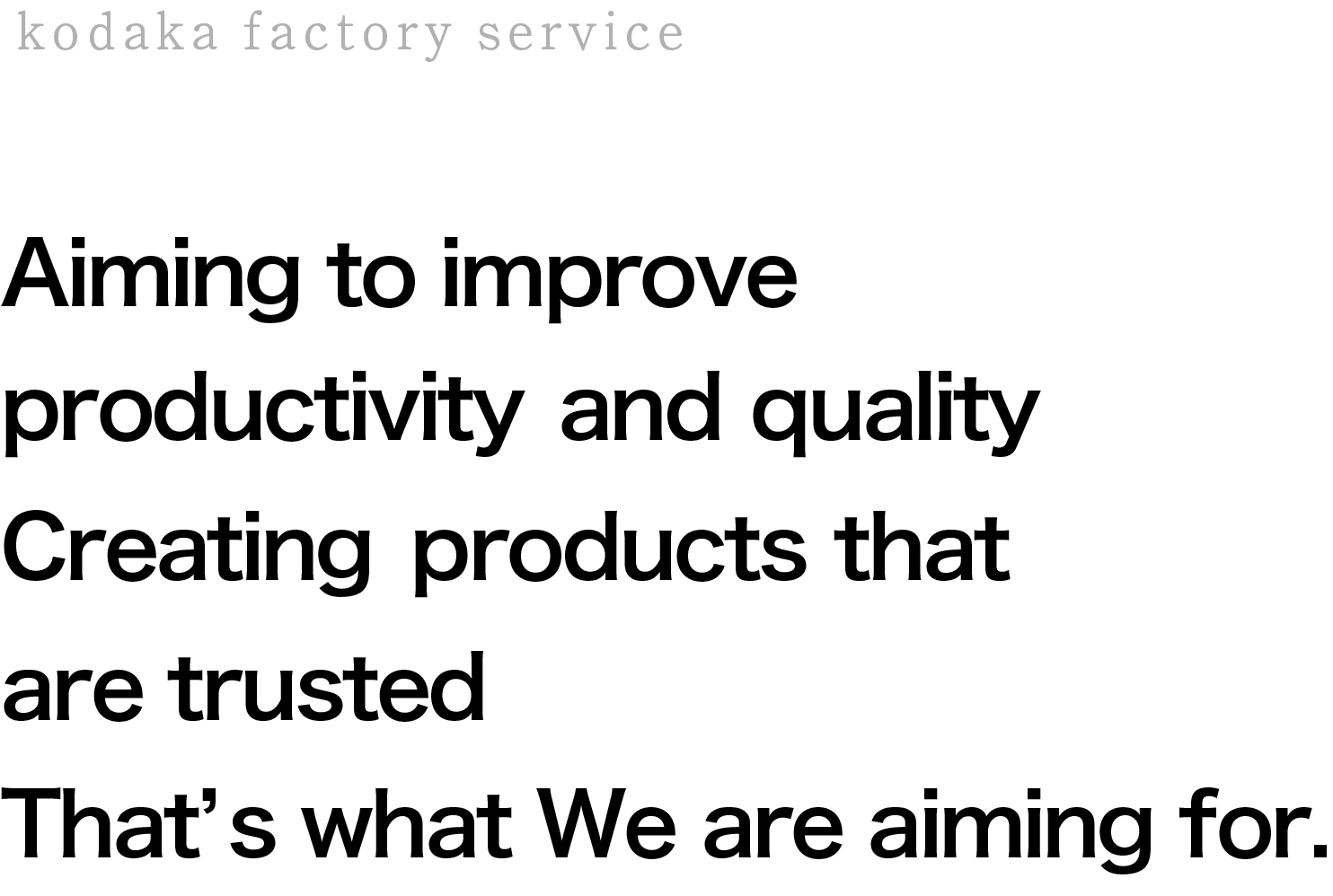
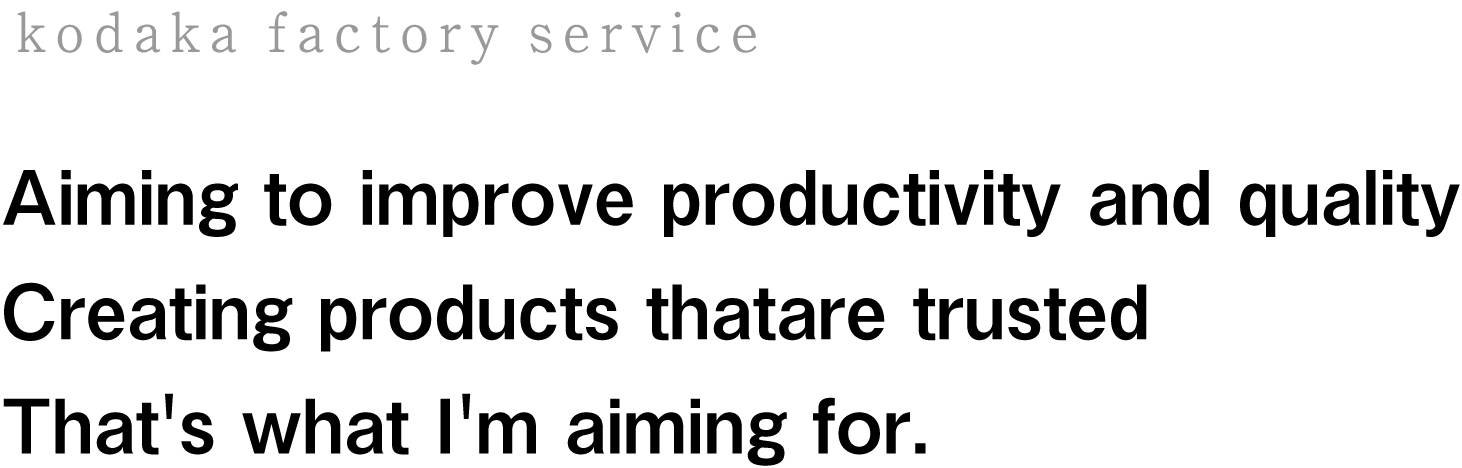
We start by understanding our customers’ needs, and set a quality goal of “establishing and maintaining a system that continues to aim for higher quality.”We supply high-quality pressed parts by putting our customers’ needs first. In addition, we have acquired ISO 9001-2015 certification, carry out environmentally friendly green procurement, and conduct production activities that take into consideration the environment based on various regulations.

KODAKA holds a discussion with the client from the initial design stage.
Our high quality dies are supported by rich experience and technical expertise. We spare no effort to achieve efficiency and reliability and manufacture quality prducts at low cost because we are convinced that our effort will be rewarded in the long run. That is, winning the customer’s trust.

Design meeting
After identifying the problems of product shape at the development stage and studying the measures to be taken, we provide the customer with solutions to shorten lead time, reduce costs, and stabilize and improve quality.
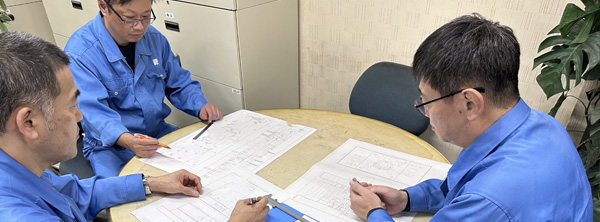

Designing tandem and progressive dies
We design dies in an accurate yet expeditious manner from prototyping to mass production on the basis of our accumulated design data and long years of experience, with product precision, workability, die maintenance, production budget, etc. in mind.
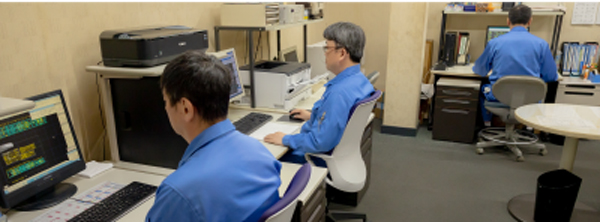

Manufacturing single and progressive dies
We manufacture dies with great precision according to the punch, die, and plate drawings prepared by the Design Section and then assemble them while adjusting each part. Metal workers having accumulated data and technical expertise add the final touches to the dies to increase the precision. Factory layout with improved workability and productivity in mind.


Punching test
After conducting punching test on an assembled die to check the dimensions, we immediately give feedback to the Design Section on some problems with the product dimensions, workmanship, and workability. We review the design, modigy the die, and perform fine tuning. We increase the precision by repeating this process a few times to obtain a reliable product.
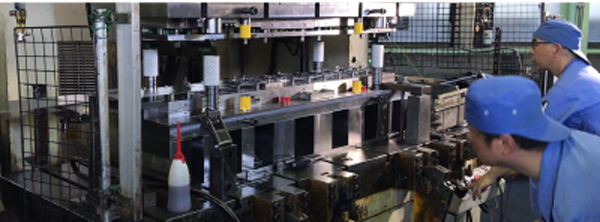

Perfoming dimensional measurements
Performing dimensional measurements is the final process after the preparation of the die drawings, machining, die assembly, and punching test. Many of the products are measured with a special inspection jig. We check the measuring points and procedures at the design meeting. We will deliver your order on the designated delivery date.
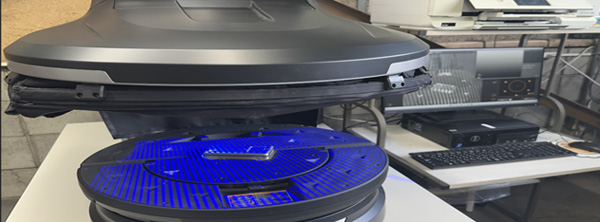
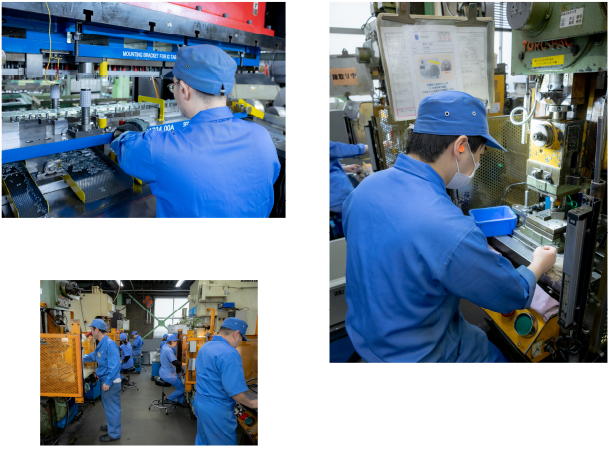
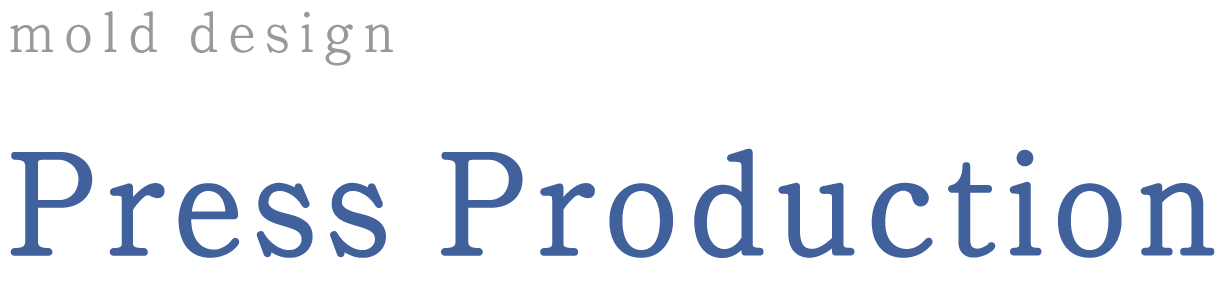
We manufacture products under thorough quality control.
Excellent technology, quality products, and thorough quality control: they are created by manufacturing engineers. Kodaka places emphasis on communication with each employee and attempts to get the most out of their talent to manufacture reliable products.
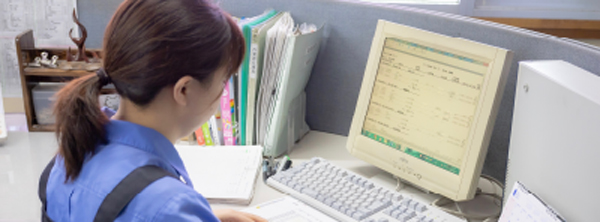

Placing and receiving orders
Our original computerized ordering system has enabled us to collectively manage a high-volume production order placed by a customer from receipt of the order to shipment. Under the Material Requirements Planning(MRP) system, the instructions on the quantity and delivery date of raw material, press working, welding, and shipping inspection will be given to each subcontractor, and thus we can meet the customer’s designated delivery date.
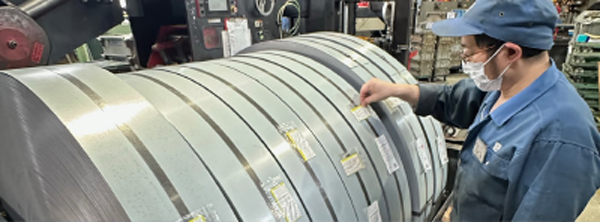

Receiving material
Materials such as coils, standard-length sheets, and cut-length sheets are available in short delivery time. The date of purchase and quantity are decided under the MRP system and a “material label” is issued when the material is delivered to us. The label contains information such as the type of material, material thickness, material widht, weight, and how many units can be produced from one material. After checking the actual material against the label, we accept it. We use the label to identify and manage materials.


Tandem press
In press working with a 25ton to 110ton tandem press machine, our skilled workers perform day-to-day operations with safety, productivity, and strict observance of delivery date in mind, paying particular attention to quality. Our press machines are equipped with PSDI (Presence Sensing Device Initiation), which is a safety device intended to improve safety, workability,and productivity.
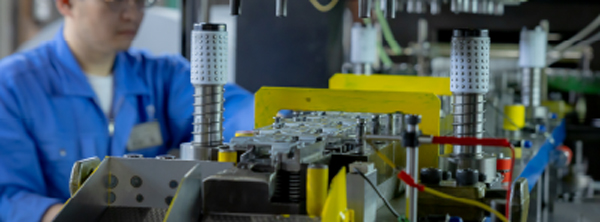

Progressive die press
In press working with a 45ton to 300ton progressive machine, we manage dimensional precision and stably supply parts with an eye to shortening lead time, improving productivity, and reducing costs by performing semi or fully-progressive processing.
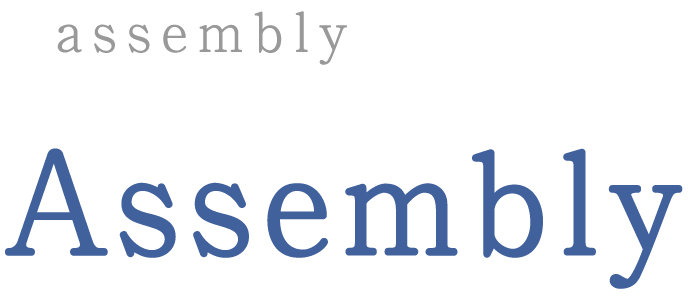
We are aiming at manufacturing reliable products, paying particular attention to productivity and quality.
Kodaka’s experienced personnel are working to improve efficiency, productivity, and dimensional precision to satisfy the customers.

Spot/projection welding
Welding parameters for spot or projection welding such as electric current and electrode force are determined depending on the material type and thickness of metal stampings. Weld strength verification test is conducted at the predetermined number of welding shots to guarantee weld strength. Each spot welding machine is provided with a spotless device.
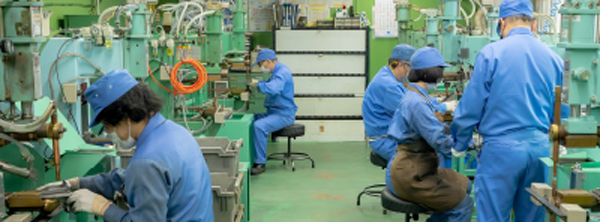

Robot CO2 gas shielded arc welding
In CO2 gas shielded arc welding, we fully discuss the specifications of stampings with the customer at the design stage, and then we decide the welding parameters, clamping jig setting position, jigs used to check for welding destortions, and quality control criteria.
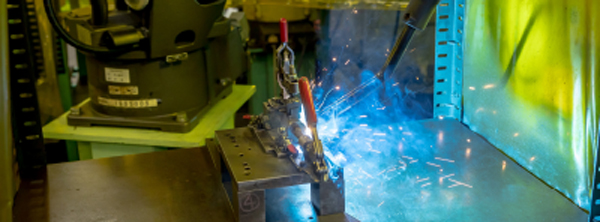

Swaging and assembling
After swaging and assembling stampings and performing operation check, we deliver finished products to the customer as requested.
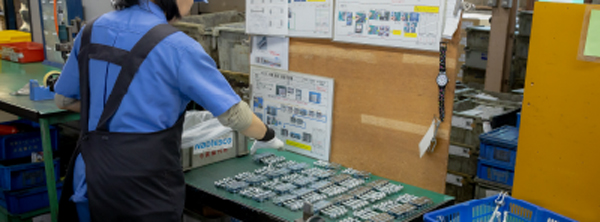
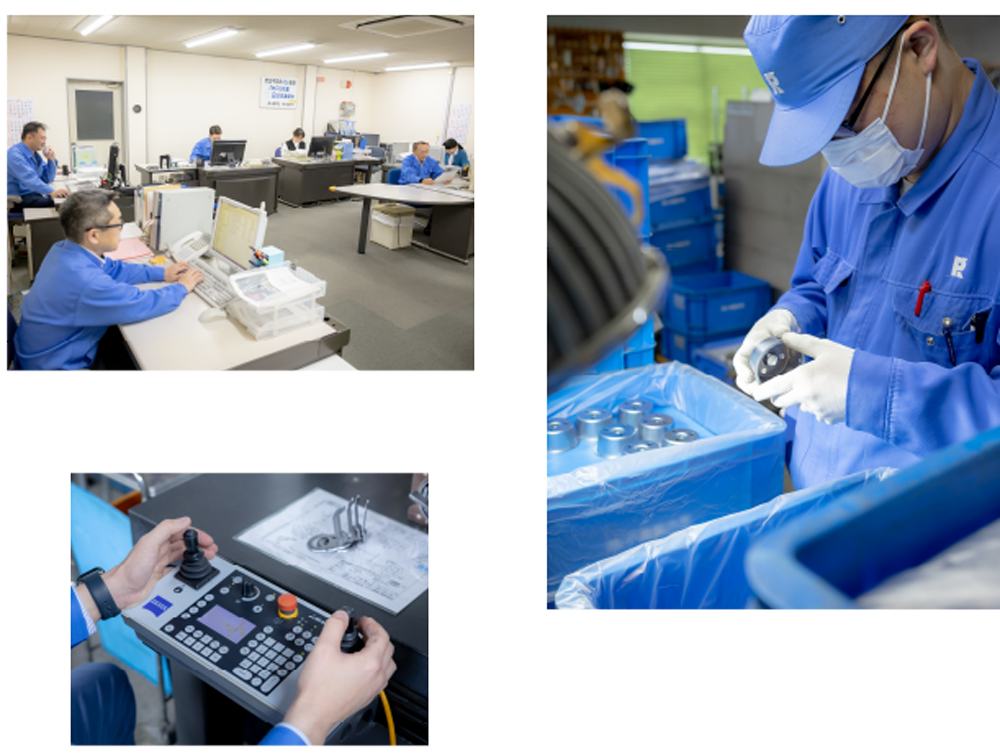
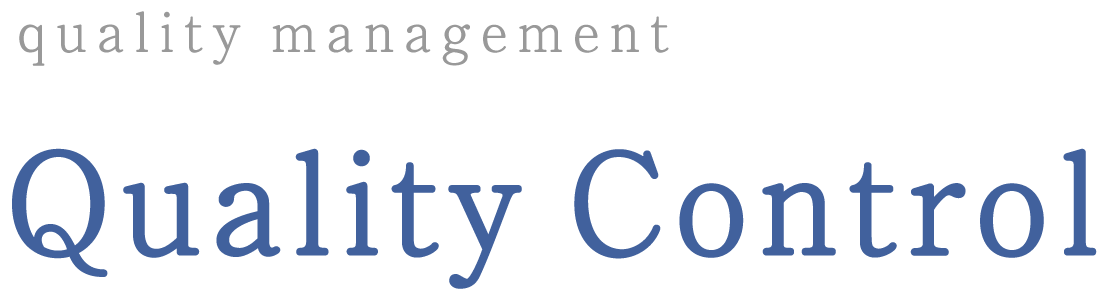
We supply reliable products manufactured under our established, strict quality control system.
In total management from die manufacture to product delivery to the customer, we fully understand the customer’s requirements and make every effort to perform strict quality control, Constant communication with the Production Division is maintained to create an ideal working environment.
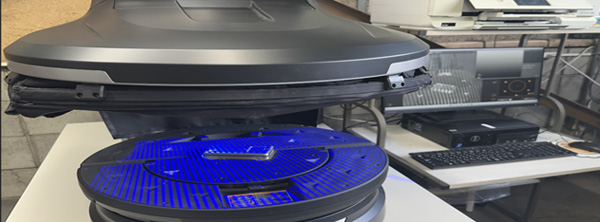
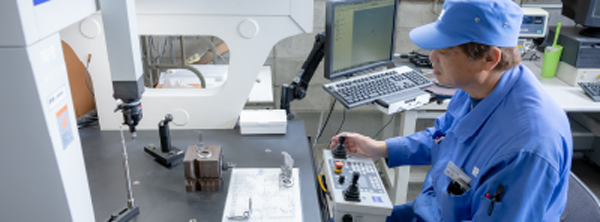

High-accuracy measuring technology
Our experienced workers measure prototype dies, mass-produced sample products, mass-produced stampings, and pressed assemblies on a day-to-day basis with a critical eye.
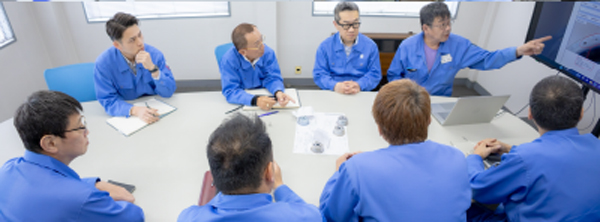

High reliability is what we always pursue.
We have frank descussions with the customer to meet ever-increasing quality requirements.
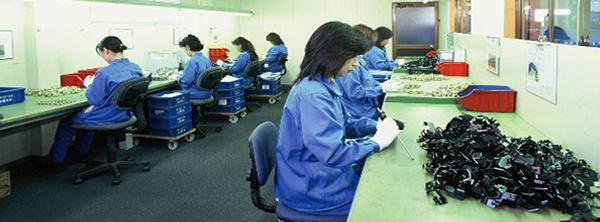

Final visual inspection
All products to be delivered to customer are subjected to close inspection: even very tiny defects cannot escape detection.
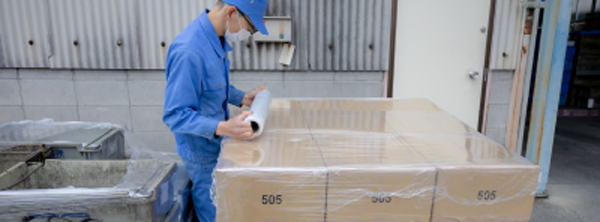

Shipping management(Prodction Management Division)
Customers may request us to shorten lead time or increase order quantity after they have placed an order, In spite of a tight schedule, we are always
working hard to manufacture high-quality products and deliver the order on the designated delivery date.